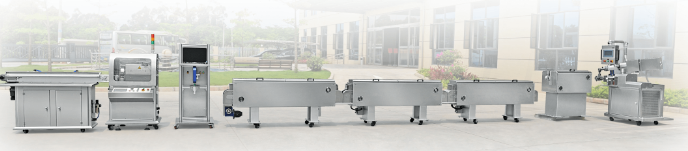
Plastic Profile Extruder: Everything You Need to Know
Plastic profile extruders play a significant role in the manufacturing industry, shaping various plastic materials into specialized profiles for diverse applications. This post provides an in-depth exploration of plastic profile extruders, how they work, their recyclability, and the wide range of applications they cater to.
What is A Plastic Profile Extruder?
A Plastic Profile Extruder is a specialized machine used in the plastics industry to produce plastic profiles, also known as extrusions. These extrusions are continuous shapes with a consistent cross-section that can vary in complexity, such as pipes, tubes, rods, channels, and various custom profiles. The extrusion process involves forcing molten plastic through a die, which imparts the desired shape as it cools and solidifies.
How Does A Plastic Profile Extruder Work?
The plastic profile extrusion process is an intricate combination of science and engineering. It begins with raw plastic materials, typically in the form of pellets or granules. These materials are fed into the extruder's hopper, where they are conveyed to the barrel through a screw mechanism. The barrel houses a heating element that melts the plastic as it progresses through the extruder.
As the molten plastic moves forward, it undergoes intense pressure from the rotating screw, ensuring uniformity and consistency in the material. The plastic is then forced through a carefully designed die, which determines the shape and dimensions of the final profile.
After exiting the die, the profile passes through a cooling system, solidifying into its desired form. Finally, the extruded profile is cut to the desired length and collected for further processing or utilization.
In summary, the extrusion process begins with raw plastic material, typically in the form of pellets or granules, being fed into the extruder's hopper. Inside the extruder, the plastic is heated and melted to a controlled temperature to become a molten mass. The molten plastic is then forced through a die, which is a specially designed-opening that shapes the plastic into the desired profile.
As the molten plastic moves forward, it undergoes intense pressure from the rotating screw, ensuring uniformity and consistency in the material. The plastic is then forced through a carefully designed die, which determines the shape and dimensions of the final profile.
After exiting the die, the profile passes through a cooling system, solidifying into its desired form. Finally, the extruded profile is cut to the desired length and collected for further processing or utilization.
In summary, the extrusion process begins with raw plastic material, typically in the form of pellets or granules, being fed into the extruder's hopper. Inside the extruder, the plastic is heated and melted to a controlled temperature to become a molten mass. The molten plastic is then forced through a die, which is a specially designed-opening that shapes the plastic into the desired profile.
Are Plastic Profiles Recyclable?
The recyclability of plastic profiles produced by extruders largely depends on the type of plastic used. Some plastics are easily recyclable, while others may pose challenges.
Common recyclable plastics include Polyethylene (PE), Polypropylene (PP), and Polystyrene (PS). However, plastics with additives or composite materials might be harder to recycle.
Common recyclable plastics include Polyethylene (PE), Polypropylene (PP), and Polystyrene (PS). However, plastics with additives or composite materials might be harder to recycle.
What Are The Common Applications of Plastic Profiles Produced By Extruders?
The plastic profiles extruders can be applied into many fields. Here are the major applications of the plastic profiles extruders.
●Automotive: Plastic profiles find applications in the automotive sector, providing solutions for door trims, window seals, weatherstrips, and interior/exterior trims. Their lightweight nature and design flexibility contribute to improved fuel efficiency and overall vehicle performance.
●Packaging: Plastic profiles are utilized in various packaging solutions, such as edge protectors, corner guards, and pipe covers. These profiles help safeguard goods during transit and minimize damage risks, making them indispensable in the logistics industry.
●Electrical and Electronics: Extruded plastic profiles play a crucial role in electrical enclosures, cable channels, and wire management systems. Their insulating properties and customized designs facilitate efficient organization and protection of electrical components.
●Consumer Goods: Plastic profiles are used in manufacturing household items like furniture trims, shelves, and storage components. Their ability to mimic the appearance of more expensive materials adds aesthetic value to consumer products.
●Automotive: Plastic profiles find applications in the automotive sector, providing solutions for door trims, window seals, weatherstrips, and interior/exterior trims. Their lightweight nature and design flexibility contribute to improved fuel efficiency and overall vehicle performance.
●Packaging: Plastic profiles are utilized in various packaging solutions, such as edge protectors, corner guards, and pipe covers. These profiles help safeguard goods during transit and minimize damage risks, making them indispensable in the logistics industry.
●Electrical and Electronics: Extruded plastic profiles play a crucial role in electrical enclosures, cable channels, and wire management systems. Their insulating properties and customized designs facilitate efficient organization and protection of electrical components.
●Consumer Goods: Plastic profiles are used in manufacturing household items like furniture trims, shelves, and storage components. Their ability to mimic the appearance of more expensive materials adds aesthetic value to consumer products.
Conclusion
Plastic profile extruders have revolutionized the manufacturing landscape, offering unparalleled versatility and efficiency in shaping plastic materials.
As the industry progresses, advancements in materials and technology will continue to drive the use of plastic profiles, providing innovative solutions across various sectors while maintaining focus on sustainability and environmental responsibility.
As the industry progresses, advancements in materials and technology will continue to drive the use of plastic profiles, providing innovative solutions across various sectors while maintaining focus on sustainability and environmental responsibility.