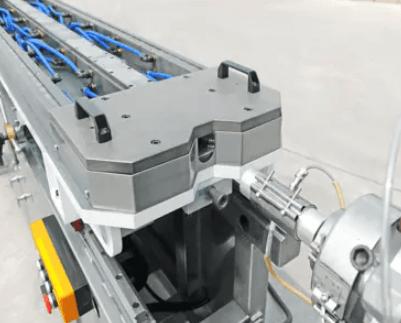
Benefits of Investing in Plastic Profile Extruders
The medical industry heavily relies on plastic components for the manufacturing of various medical devices. Plastic profile extruders play a vital role in this process, enabling the production of precise and customized plastic profiles that meet the specific requirements of medical applications. In this article, we will explore the numerous benefits of investing in plastic profile extruders for medical device manufacturers.
Understanding Plastic Profile Extruders
Plastic profile extruders are machines designed to shape thermoplastic materials into continuous profiles of various shapes and sizes. The extrusion process involves heating the plastic material and forcing it through a die, resulting in a consistent and continuous profile. This process is highly relevant to the medical device manufacturing industry as it allows for the creation of complex profiles required for medical applications. Plastic profile extruders come in different types, each offering unique capabilities suited for specific medical device requirements.
Enhanced Precision and Customization
One of the significant benefits of plastic profile extruders is their ability to create profiles with exceptional precision. The extrusion process allows for tight control over dimensions, ensuring consistent and accurate profiles. Medical devices often have strict specifications, and the precision offered by plastic profile extruders helps manufacturers meet these requirements precisely.
Furthermore, customization is essential in the medical industry to accommodate the diverse needs of patients and medical professionals. Plastic profile extruders enable manufacturers to produce customized profiles tailored to specific medical applications. Whether it is a unique shape, size, or functionality, plastic profile extruders provide the flexibility to meet the demands of medical device customization. This level of precision and customization ensures that medical devices are well-suited for their intended purposes, enhancing patient care and safety.
Furthermore, customization is essential in the medical industry to accommodate the diverse needs of patients and medical professionals. Plastic profile extruders enable manufacturers to produce customized profiles tailored to specific medical applications. Whether it is a unique shape, size, or functionality, plastic profile extruders provide the flexibility to meet the demands of medical device customization. This level of precision and customization ensures that medical devices are well-suited for their intended purposes, enhancing patient care and safety.
Cost-Effectiveness and Time Efficiency
Investing in plastic profile extruders can bring substantial cost savings to medical device manufacturers. Compared to other manufacturing methods, such as injection molding, plastic profile extrusion offers advantages in terms of material utilization and reduced waste. The extrusion process generates minimal scrap, maximizing material usage and minimizing costs associated with material waste.
Moreover, plastic profile extruders contribute to time efficiency in medical device manufacturing. The continuous production capability of extrusion allows for high-volume production, ensuring a faster turnaround time. Manufacturers can meet increasing demands and reduce production lead times, ultimately improving overall operational efficiency.
Moreover, plastic profile extruders contribute to time efficiency in medical device manufacturing. The continuous production capability of extrusion allows for high-volume production, ensuring a faster turnaround time. Manufacturers can meet increasing demands and reduce production lead times, ultimately improving overall operational efficiency.
Material Compatibility and Versatility
Plastic profile extruders support a wide range of thermoplastic materials, providing manufacturers with the flexibility to choose the most suitable material for their medical device applications. Different materials possess unique properties such as flexibility, rigidity, transparency, and chemical resistance. Plastic profile extrusion enables the production of profiles from materials that comply with specific medical industry standards and regulations.
For instance, medical tubing used in intravenous lines requires a high level of flexibility and biocompatibility. Plastic profile extruders allow manufacturers to produce tubing profiles using materials like PVC, PE, or TPU, which meet the stringent requirements for patient safety and regulatory compliance. The versatility of plastic profile extruders ensures that medical devices can be fabricated from materials that best suit their intended use.
For instance, medical tubing used in intravenous lines requires a high level of flexibility and biocompatibility. Plastic profile extruders allow manufacturers to produce tubing profiles using materials like PVC, PE, or TPU, which meet the stringent requirements for patient safety and regulatory compliance. The versatility of plastic profile extruders ensures that medical devices can be fabricated from materials that best suit their intended use.
Consistency and Quality Control
Consistency is crucial in the medical industry to ensure that devices perform reliably and meet regulatory standards. Plastic profile extruders play a significant role in maintaining consistent dimensions and properties of medical device components. Extrusion machines are calibrated precisely to produce profiles with consistent shapes, sizes, and material properties.
Additionally, plastic profile extruders incorporate quality control measures throughout the extrusion process. Monitoring systems track various parameters such as temperature, pressure, and speed to ensure consistent quality. Manufacturers can have confidence in the reliability and uniformity of the profiles produced, reducing the risk of device failure and enhancing patient safety.
Additionally, plastic profile extruders incorporate quality control measures throughout the extrusion process. Monitoring systems track various parameters such as temperature, pressure, and speed to ensure consistent quality. Manufacturers can have confidence in the reliability and uniformity of the profiles produced, reducing the risk of device failure and enhancing patient safety.
Regulatory Compliance and Safety
The medical industry is subject to strict regulatory requirements to ensure patient safety. Investing in plastic profile extruders helps medical device manufacturers meet these stringent regulations and achieve regulatory compliance.
Plastic profile extruders enable the production of medical device components with materials that adhere to specific regulatory guidelines. These guidelines may include biocompatibility, sterilization compatibility, and chemical resistance, among others. By utilizing the appropriate materials through plastic profile extrusion, manufacturers can ensure that their devices meet the necessary regulatory standards, reducing the risk of adverse reactions and ensuring patient safety.
Furthermore, plastic profile extruders contribute to the overall safety of medical devices by offering enhanced design capabilities. The precise control over the extrusion process enables the creation of profiles with features that promote safety and functionality. For example, extruded profiles can incorporate channels for precise fluid flow, integrated connectors for secure device assembly, and textured surfaces for improved grip and ergonomics. Plastic profile extrusion allows for the production of intricate designs that enhance the usability and safety of medical devices.
Plastic profile extruders enable the production of medical device components with materials that adhere to specific regulatory guidelines. These guidelines may include biocompatibility, sterilization compatibility, and chemical resistance, among others. By utilizing the appropriate materials through plastic profile extrusion, manufacturers can ensure that their devices meet the necessary regulatory standards, reducing the risk of adverse reactions and ensuring patient safety.
Furthermore, plastic profile extruders contribute to the overall safety of medical devices by offering enhanced design capabilities. The precise control over the extrusion process enables the creation of profiles with features that promote safety and functionality. For example, extruded profiles can incorporate channels for precise fluid flow, integrated connectors for secure device assembly, and textured surfaces for improved grip and ergonomics. Plastic profile extrusion allows for the production of intricate designs that enhance the usability and safety of medical devices.
Future Trends and Innovations
The field of plastic profile extrusion is constantly evolving, and emerging technologies and innovations are poised to further enhance its benefits in the medical industry. Automation and artificial intelligence (AI) are expected to play a significant role in improving the efficiency and precision of plastic profile extrusion processes. Automated control systems can monitor and adjust process parameters in real-time, optimizing production and ensuring consistent quality. AI algorithms can analyze data collected during extrusion to identify patterns and make predictive adjustments, further improving product quality and reducing waste.
Additionally, advancements in materials science continue to expand the range of thermoplastic materials available for plastic profile extrusion. This allows for the development of profiles with advanced properties, such as antimicrobial surfaces, conductive elements for electronic integration, or biodegradable materials for environmentally friendly devices. These innovations open up new possibilities for medical device design and functionality.
Additionally, advancements in materials science continue to expand the range of thermoplastic materials available for plastic profile extrusion. This allows for the development of profiles with advanced properties, such as antimicrobial surfaces, conductive elements for electronic integration, or biodegradable materials for environmentally friendly devices. These innovations open up new possibilities for medical device design and functionality.
Conclusion
Investing in plastic profile extruders brings numerous benefits to the medical device manufacturing industry.
As the field of plastic profile extrusion continues to advance, with emerging technologies and materials, the potential for further improvements and innovations in the medical industry is promising. By embracing the benefits of plastic profile extruders, medical device manufacturers can enhance their competitiveness, drive innovation, and ultimately improve patient care and outcomes.
As the field of plastic profile extrusion continues to advance, with emerging technologies and materials, the potential for further improvements and innovations in the medical industry is promising. By embracing the benefits of plastic profile extruders, medical device manufacturers can enhance their competitiveness, drive innovation, and ultimately improve patient care and outcomes.